浅谈机器人打磨应用——打磨的基础认知
打磨在工业中是一个涉及面广,极其繁化,又相对小众的行业。——通俗来讲,对于劳动者,打磨的车间环境恶劣,噪音大,粉尘污染严重,而且工作强度高,如此长久作业极易造成劳动者双耳失聪,粉尘病等各种职业病。在规范化企业,一般打磨工人的职业生涯为2~3年。而随着网络时代的到来,新兴行业例如直播和外卖,使得过去很容易源源不断的招到的打磨工,变得难以续接。——综上原因,打磨迈向自动化是工业发展不可阻挡的历程。目前
前言:打磨在工业中是一个涉及面广,极其繁化,又相对小众的行业。
——通俗来讲,对于劳动者,打磨的车间环境恶劣,噪音大,粉尘污染严重,而且工作强度高,如此长久作业极易造成劳动者双耳失聪,粉尘病等各种职业病。在规范化企业,一般打磨工人的职业生涯为2~3年。而随着网络时代的到来,新兴行业例如直播和外卖,使得过去很容易源源不断的招到的打磨工,变得难以续接。
——综上原因,打磨迈向自动化是工业发展不可阻挡的历程。目前我国以机器人替代工人打磨的成熟方案比较少,但是很多主营焊接的集成商公司正在探索,也有不少成功案例。
——最后祝愿打磨行业越来越成熟,国家繁荣兴盛,个人都能安居乐业。
——以下介绍笔者个人工作经历中网络搜寻和书本阅读所认识到的一些基础认知汇总,如有错误,还望不吝提醒——2022.9.27首写
参考资料:GB/T 16458–2021
一、常见的打磨术语
1、打磨
通过磨具的物理接触来使得材料获取特定表面粗糙度1
2、粗糙度
表面粗糙度Ra、Rz、Ry是评定物体表面质量的一项技术指标。2
3、磨粒(矿砂)
磨粒是用人工方法制成特定的粒度,用以制造切除材料余量的磨削、抛光和研磨工具的磨料颗粒。
4、粒度与目数(粒度号)
粒度:磨粒尺寸大小的量度
目数:按照执行标准对粒度所做的分级标志3
5、磨料(磨具)
用磨粒制作而成的用于磨削(包括研磨和抛光)和切割的材料
6、硬度
磨粒在外力作用下从磨具表面脱落的难易程度
7、相对硬度
磨粒相对于被打磨材料的硬度
8、自锐性
磨料在使用过程中保持切削能力的性能
9、结合剂
将磨粒固结成磨具的材料
10、固结类磨料
由结合剂将磨粒固结成一定形状具有一定强度的磨具4
11、电镀类磨料
采用电镀工艺制成的超硬磨料磨具5
12、涂附类磨料
用黏结剂把磨粒粘附在可挠曲的基材上制成的磨料6
13、黏结剂
涂附磨具中粘接磨粒和基材用的材料
14、基材
涂附磨具中磨粒和粘结剂的承载体
15、松散类磨料
磨粒以自由状态存在的无固定形状的磨料7
二、常见的打磨工艺
常见的打磨工艺总的可以归为两大类:表面处理和余量去除
那么何谓“表面处理” 何谓“余量去除”呢?
笔者的判断方法就是,使用同一种磨料,对整个平面的处理,为表面处理;反之使用磨料单独对平面的某个突出部位进行处理,为余量去除。
表面处理何余量去除,细化下来有很多种分类,以下介绍常见的几种。
表面处理
1、表面砂光
砂光是利用砂砾的切削作用将材料表面的加工痕迹、毛刺、污迹等加工光滑;砂光工艺就好比是将高山全部削平,这样就能使得地面看上去很是平整;
2、表面抛光
抛光是利用抛光蜡填平材料表面的坑凹,使工件表面粗糙度降低,材料表面更加平整,以获得光亮、平整表面的加工方法
3、表面砂糙/拉毛
拉毛主要是针对暴露在大气环境中时间过长的转换型涂层(如醇酸、环氧、聚氨脂等)做出的一种表面处理的方式,其主要目的是为了得到良好的表面粗糙度,减少表面杂质和去除粉化层,作用在于和施工涂层具有良好层间附着力。"
非转换型涂料,如丙烯酸、乙烯、氯化橡胶等,重新涂装时不需要‘拉毛’,因为涂料中的溶剂能溶解老涂层的表面,新老涂层产生互溶,确保层间的附着力
4、 表面拉丝
表面拉丝处理是通过研磨产品在工件表面形成线纹,起到装饰效果的一种表面处理手段。在不锈钢行业常见
5、去除涂层/除锈
去除涂层和除锈的目的是使被涂物表面光滑、清洁,增加涂料与被涂表面的附着力,充分发挥 涂料抵抗腐蚀的能力
余量去除
去除飞边(合模线)、浇口去除、焊缝打磨8、机加工毛刺、导角、去除氧化皮
三、常见的打磨前后道工艺
打磨前道工艺决定了打磨的可行性与打磨难度,而打磨的后道工艺决定了打磨的验收标准。
常见的打磨前道工艺为:铸造、焊接、切割、复合材料、机加工、3D打印、批腻子等等
常见的打磨后 道工艺为:不处理(例如拉丝)、喷涂、电镀、喷砂/喷丸
四、常见的打磨工具
目前市面上常见的打磨工具根据动力源不同,分为两种:气动、电动。
气动打磨工具:价格便宜,打磨效率偏低,寿命不长、多用于表面处理。
电动工具:价格偏高,打磨效率高,寿命长,可用于表面处理亦可用于余量去除。
常见的气动打磨工具,例如风磨机、气动锉刀,气动笔,气动主轴。
常见的电动打磨工具,永磁同步电机,伺服电机。
五、用于机械臂打磨的辅助设备
自动化打磨应用中,要使机械臂进行打磨作业,除了保证机械臂模拟人类的动作,并且需要跟人一样感知。人通常具备五种感官(视觉,听觉,味觉,嗅觉,触觉)
而在打磨作业的过程中,劳动者通常使用到两种感官,触觉和视觉。触觉(力大小,粗糙度)实施打磨;视觉(镜面,哑光,高度,厚度)验证打磨。
工业机械臂打磨应用中,机器人的视觉通常是视觉相机、定位激光,测距仪、粗糙度测试仪等设备,机械臂的触觉则为力控设备代替。
视觉笔者了解甚少,此处主要介绍力控设备
机械臂力控制大体上可以分为两类,关节力控制9和末端力控制10,其中关节力控制指机器人各关节均具备一个力/力矩传感器,而末端力控制指机器人末端装有一个力传感器(1~6维传感器)。
六、国内外力控设备厂商
国外
柔顺力控制:Ferrobotics、Pushcorp
六维力:ATI
径向浮动:Amtru
国内
柔顺力控制:无锡盈连科技
六维力:宇立
径向浮动:
七、国内外力控设备优缺点
利益相关,内容笔者离开相关行业再补充
八、国内外专业打磨集成商
利益相关,内容笔者离开相关行业再补充
九、打磨磨料国内外厂家
国外
3M、赫美斯、鹿牌、诺顿、圣戈班、
国内
上述国外厂商代工厂。
-
打磨与铣削的差别是什么 ?
打磨侧重于产品的外表面的修整,强调触摸,观感效果
铣削则是将产品加工到指定尺寸,强调尺寸精准 ↩︎ -
2.1轮廓算术平均偏差Ra
指在一定取样长度内,轮廓上各点刀轮廓中线距离绝对值的平均值(不能用作太过粗糙或台光滑的表面的评定参数
2.2微观不平度十点平均高度Rz
指在取样长度内5个最大的轮廓峰高平均值与5个最大轮廓谷深平均值之和
2.3 轮廓最大高度Ry
在取样长度内,轮廓的峰顶线与谷底线之间的距离
2.4 粗糙度的测量方法
比较法
将被测表面和表面粗糙度样板直接进行比较、多用于车间,评定表面粗糙度值较大的工件
光切法
利用光切原理,用双管显微镜测量。常用于测量Rz为0.5~60μm
干涉法
利用光波干涉原理,用干涉显微镜测量。可测量Rz和Ry值
针描法
是利用金刚石触针在被测表面上轻轻划过,从而测出表面粗糙度Ra值的一种方法
2.5 表面粗超度性能影响
影响耐磨性
表面粗糙度太大和太小都不耐磨。表面越粗糙,配合表面的有效接触面积越小,压强越大,摩擦阻力越大,磨损久越快。表面粗糙度太小,也会导致磨损加剧,因为表面太光滑,存不住润滑油,接触面间不易形成油膜,容易发生分子间粘结而加剧磨损
影响配合稳定性
对间隙配合来说,表面越粗糙,就越易磨损,使工作过程中间隙逐渐增大;对于过盈配合来说,由于装配时将微观凸峰挤平,减小了实际有效过盈,降低了连接强度。
影响疲劳强度
粗糙零件的表面存在较大波谷,它们像尖角缺口和裂纹一样,对应力集中很敏感,从而影响零件疲劳强度
影响耐腐蚀性
粗糙的零件表面,易使腐蚀性气体或液体通过表面的微观凹谷渗入到金属内层,造成表面腐蚀
影响密封性
粗糙表面之间无法严密贴合,气体或液体通过接触面间缝隙渗漏
影响接触刚度
接触刚度时零件接合面在外力作用下,抵抗接触变形的能力,机器的刚度很大程度上取决于各零件之间的接触刚度
影响测量精度
零件被测表面和测量工具测量面的粗糙度都会直接影响测量精度,尤其是在精密测量
2.6 不同打磨对应的Ra粗糙度(仅供参考)
一般打磨
R a1.25~0.16微米
精密打磨
R a0.16~0.04微米
超精密打磨
R a0.04~0.01微米
镜面打磨
可达 R a0.01微米以下 ↩︎ -
砂纸目数与表面粗糙度的关系
耗材的粒度等级越高,打磨出来的效果越细腻↩︎
-
常见的固结磨料
砂轮、磨头、磨石、金刚石砂轮、立方氮化硼砂轮 ↩︎ -
常见的电镀类磨料
电镀金刚石砂轮、电镀金刚石什锦搓 ↩︎ -
常见的涂附类磨料
砂带、砂纸卷、砂纸、砂页轮(千叶轮)、百叶片 ↩︎ -
常见的松散类磨料
研磨膏、研磨液、抛光膏、抛光蜡、抛光液 ↩︎ -
激光焊缝、点焊、弧焊、透焊痕迹处理 ↩︎
-
例如:电流环反馈控制,大致原理为采集机械臂六轴的电流大小,通过算法换算出当前末端力大小。优点是无需安装额外设备,减轻机械臂负重,打磨工具干涉较少。缺点是单纯以电流环反馈,难以稳定输出机械臂末端输出的力,负载较小,对机械臂运行速度有限制,技术不成熟。 ↩︎
-
例如:六维力控制,通过末端安装六维力传感器,反馈给机器人,机器人再进行相应的动作调整末端输出力。优点是可以输出六维力(x,y,z,rx,ry,rz),缺点是传感器需要能在机器人系统中配置,负载较小,价格昂贵,对机械臂运行速度有限制,人工调试难度高。因为是依靠机器人本体动作来调整输出力大小,调试过程中有时会出现一些不可控的机器人动作(笔者亲历)
例如:柔顺力控制,通过末端安装力执行器,机器人只需要将输出力大小下发给力控制器,力执行器(一般为气驱动,也有电机驱动的)自动输出相应力大小,且打磨工具可随着工件表面起伏而随之贴合。优点是输出力值稳定,适应性更强,负载高,机械臂运行速度无限制,调试方便,技术成熟。缺点:一般只有一维力,设备尺寸较大,对于复杂工件容易干涉。 ↩︎
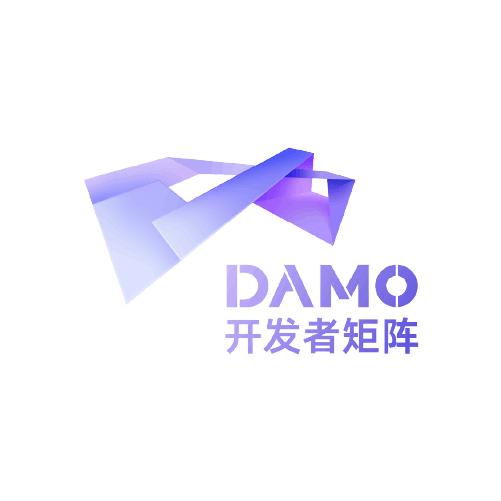
DAMO开发者矩阵,由阿里巴巴达摩院和中国互联网协会联合发起,致力于探讨最前沿的技术趋势与应用成果,搭建高质量的交流与分享平台,推动技术创新与产业应用链接,围绕“人工智能与新型计算”构建开放共享的开发者生态。
更多推荐
所有评论(0)