晶圆与芯片生产工艺流程详解
本文还有配套的精品资源,点击获取简介:本文详细介绍了电子行业中晶圆和芯片的生产工艺流程,是现代半导体器件制造的基础。从硅晶圆的生长到集成电路的封装测试,每一步都需精确控制以保证芯片性能和可靠性。工艺流程的不断优化,旨在提高芯片的集成度、速度和能效,满足市场日益增长的需求。1. 硅锭生长技术硅的提炼与纯化半导体工业的核心原料是高纯度的单晶硅。硅的...
简介:本文详细介绍了电子行业中晶圆和芯片的生产工艺流程,是现代半导体器件制造的基础。从硅晶圆的生长到集成电路的封装测试,每一步都需精确控制以保证芯片性能和可靠性。工艺流程的不断优化,旨在提高芯片的集成度、速度和能效,满足市场日益增长的需求。
1. 硅锭生长技术
硅的提炼与纯化
半导体工业的核心原料是高纯度的单晶硅。硅的提炼过程始于从沙子中提取二氧化硅,然后通过化学反应将其转化为纯度较低的金属硅。金属硅经过进一步的化学处理,如反应精炼和区熔,以去除杂质,最终得到高纯度的多晶硅。这个过程对于后续的硅锭生长至关重要,因为它直接影响到最终产品的质量。
硅锭的生长
高纯度的多晶硅被用于制造单晶硅锭,这是通过晶体生长技术实现的,主要有两种方法:直拉法(CZ法)和悬浮区熔法(FZ法)。直拉法是将多晶硅熔化,然后在籽晶的引导下,缓慢地向上拉伸,形成单晶硅锭。这一过程需要严格控制温度和速度,以确保晶体结构的一致性和无缺陷。悬浮区熔法则不使用籽晶,而是通过局部加热使硅熔化,然后缓慢冷却形成单晶。
硅锭的质量检测
硅锭生长完成后,需要经过严格的质量检测。这包括光学和电子显微镜下的微观缺陷检查,以及电学性能测试。这些测试有助于识别任何可能影响最终芯片性能的缺陷。只有通过检测的硅锭才能进入下一阶段的晶圆加工。
总结 :从提炼到生长,再到检测,硅锭的生产过程是芯片制造的基础。理解这一过程对于任何希望深入了解半导体行业的人来说都是必不可少的。随着技术的发展,这些基础工艺也在不断地进行优化和创新,以满足更高性能和更低成本的需求。
2. 晶圆加工工艺
2.1 晶圆切割及其规格
2.1.1 切割技术的基本原理
晶圆切割是晶圆加工中的关键步骤,它涉及到将大尺寸的单晶硅锭切割成小块的晶圆片,以便进一步加工。切割技术的基本原理是利用机械或激光的方式在晶圆表面形成微小的切割线,然后通过物理或化学方法使晶圆沿着这些切割线断裂。机械切割通常使用钻石刀轮,而激光切割则利用激光束的高能量密度在材料内部产生热应力,从而实现切割。
2.1.2 晶圆尺寸的标准与分类
晶圆尺寸的标准是在半导体行业中经过长时间发展而形成的,主要有3英寸、4英寸、6英寸、8英寸和12英寸等规格。随着技术的进步,晶圆尺寸逐渐增大,以提高晶圆的利用率和生产效率。例如,12英寸晶圆相比8英寸晶圆,在相同的制造工艺下可以产出更多的芯片。晶圆的尺寸分类如下表所示:
| 晶圆尺寸 | 直径 (英寸) | 使用场景 | |----------|-------------|----------| | 3英寸 | 76.2 | 早期工艺 | | 4英寸 | 101.6 | 早期工艺 | | 6英寸 | 152.4 | 中等工艺 | | 8英寸 | 203.2 | 高级工艺 | | 12英寸 | 304.8 | 先进工艺 |
2.1.3 切割后晶圆的处理与检验
切割后的晶圆需要进行一系列的处理和检验步骤,以确保其质量和一致性。处理步骤包括边缘修整、表面抛光等,以去除切割过程中产生的毛刺和不平整的表面。检验步骤则包括尺寸测量、表面缺陷检查等,以确保晶圆符合后续加工的要求。晶圆切割后的处理与检验流程可以用以下的mermaid流程图表示:
graph LR
A[切割后的晶圆] --> B[边缘修整]
B --> C[表面抛光]
C --> D[尺寸测量]
D --> E[表面缺陷检查]
E --> F[合格晶圆]
2.2 晶圆清洗的重要性
2.2.1 清洗的目的与必要性
晶圆清洗是去除晶圆表面的污染物和有机物的过程,对于提高芯片的良率和性能至关重要。污染物可能来自于晶圆切割、搬运等加工步骤,也可能来自于环境中的尘埃、油脂等。不清洁的晶圆会导致光刻过程中光刻胶的不良粘附,进而影响电路图案的转移精度,最终影响芯片的性能和可靠性。
2.2.2 清洗方法的选择与应用
晶圆清洗的方法主要有物理清洗、化学清洗和超纯水清洗等。物理清洗包括刷洗、喷射清洗等,主要去除大颗粒污染物;化学清洗则使用化学试剂去除有机物、金属离子等微小污染物;超纯水清洗则用于最后的冲洗,确保晶圆表面的清洁度。以下是不同清洗方法的比较:
| 清洗方法 | 主要作用 | 特点 | |----------|----------|------| | 物理清洗 | 去除大颗粒污染物 | 清洗力度大,可能损伤晶圆 | | 化学清洗 | 去除有机物、金属离子 | 化学试剂可能残留 | | 超纯水清洗 | 冲洗残留物 | 清洁度高,不会损伤晶圆 |
2.2.3 清洗效果的评估与优化
清洗效果的评估通常采用表面分析技术,如扫描电子显微镜(SEM)、原子力显微镜(AFM)等,来观察晶圆表面的清洁程度。优化清洗效果的方法包括调整清洗剂的配比、清洗时间和温度等,以及采用更先进的清洗技术。以下是清洗效果评估的代码示例:
# 清洗效果评估代码示例
import SEM_analysis
def evaluate_cleanliness(sample):
results = SEM_analysis.scan(sample)
if results['particles'] < 100:
return '清洗效果良好'
else:
return '清洗效果需要优化'
sample = '晶圆样本'
result = evaluate_cleanliness(sample)
print(result)
此代码通过模拟的方式,展示如何利用表面分析技术评估晶圆的清洗效果。代码逻辑分析和参数说明将在后续部分详细展开。
2.3 氧化与扩散过程
2.3.1 氧化过程的原理与应用
晶圆的氧化是指在高温下,使晶圆表面与氧气或水蒸气反应,形成一层二氧化硅薄膜的过程。这层二氧化硅薄膜作为绝缘层,在芯片制造中用于隔离不同的电路层。氧化过程的原理是通过热扩散的方式,使得氧气分子渗透进入硅晶体的晶格中,形成二氧化硅。
2.3.2 扩散过程的原理与控制
扩散过程是在高温下,将掺杂元素(如硼、磷等)引入硅晶体中的过程,目的是改变硅晶体的导电性质。扩散过程的原理是通过控制温度和时间,使得掺杂元素在硅晶体中的浓度分布达到预定的电学特性。扩散过程通常分为固态源扩散和液态源扩散两种。
2.3.3 氧化与扩散的工艺整合
氧化与扩散过程在芯片制造中往往是紧密关联的。例如,在MOSFET的制造中,首先通过氧化形成栅氧化层,然后通过扩散形成源极和漏极。整合这两种工艺需要精确控制温度和时间,以确保不同层之间的绝缘和导电性能。以下是氧化与扩散工艺整合的mermaid流程图:
graph LR
A[晶圆准备] --> B[氧化形成绝缘层]
B --> C[扩散形成导电层]
C --> D[光刻形成图案]
D --> E[后续加工步骤]
在本章节中,我们介绍了晶圆加工工艺中的关键步骤,包括晶圆切割及其规格、晶圆清洗的重要性以及氧化与扩散过程。每个小节都详细分析了相关技术的原理、应用和优化方法,并通过代码示例和mermaid流程图展示了工艺流程和评估方法。这些内容对于理解芯片制造中的基础工艺至关重要。
3. 光刻与刻蚀技术
光刻与刻蚀是芯片制造过程中至关重要的步骤,它们共同决定了芯片的精细程度和最终性能。在本章节中,我们将深入探讨光刻和刻蚀技术的基本原理、工作流程、优化挑战以及湿法与干法刻蚀技术的比较。
3.1 光刻过程与技术
光刻技术是将电路图案精确转移到硅晶圆上的过程,它决定了芯片的集成度和性能。光刻过程涉及到光刻胶的涂覆、曝光、显影等步骤,每一步都必须精确控制以确保图案转移的准确性。
3.1.1 光刻的原理与流程
光刻的原理基于光的直线传播特性,通过光刻机的光学系统将掩模版上的电路图案缩小并转移到涂有光刻胶的晶圆上。这个过程通常包括以下步骤:
- 涂覆 :在晶圆表面均匀涂覆一层光刻胶。
- 前烘 :去除光刻胶中的溶剂,提高其粘附性。
- 曝光 :通过掩模版将图案转移到光刻胶上。
- 显影 :使用显影剂去除曝光区域的光刻胶,形成图案。
3.1.2 光刻机的工作原理
光刻机的核心是曝光系统,它通常包括光源、掩模版、成像透镜和晶圆载台。光源发出的光通过掩模版,掩模版上的图案被缩小并精确地投射到光刻胶上。曝光光源的波长越短,光刻的分辨率越高。
3.1.3 光刻工艺的优化与挑战
随着半导体工艺的进步,光刻技术面临着分辨率极限和成本增加的挑战。为了克服这些挑战,研究人员开发了多种技术,如浸没式光刻和极紫外光刻(EUV)。这些技术通过使用更短的波长和改进的光学系统来提高分辨率。
代码块示例
graph LR
A[涂覆光刻胶] --> B[前烘]
B --> C[曝光]
C --> D[显影]
D --> E[检查图案]
E -->|合格| F[继续后续步骤]
E -->|不合格| G[重新涂覆光刻胶]
在这个流程图中,我们展示了光刻过程的各个步骤,从涂覆光刻胶开始,到显影后的图案检查。如果图案合格,则继续后续步骤;如果不合格,则重新开始涂覆光刻胶的步骤。
3.2 刻蚀技术(湿法与干法)
刻蚀技术用于在光刻后去除晶圆上未被光刻胶保护的区域,从而形成电路图案。刻蚀分为湿法刻蚀和干法刻蚀两种主要类型。
3.2.1 湿法刻蚀的原理与应用
湿法刻蚀是使用化学溶液去除硅或其他材料的过程。这个过程的优点是成本较低,但其各向同性刻蚀特性限制了其在高精度刻蚀中的应用。
3.2.2 干法刻蚀的原理与应用
干法刻蚀则使用等离子体或离子束来去除材料,其各向异性特性使得它在高精度刻蚀中得到广泛应用。常见的干法刻蚀技术包括反应离子刻蚀(RIE)和深反应离子刻蚀(DRIE)。
3.2.3 湿法与干法刻蚀的比较与选择
湿法刻蚀和干法刻蚀各有优缺点,选择哪种技术取决于所需的精度、成本和制造效率。在实际应用中,两种技术常常结合使用,以发挥各自的优势。
表格展示
| 刻蚀类型 | 优点 | 缺点 | 应用场景 | |----------|------|------|----------| | 湿法刻蚀 | 成本低,刻蚀均匀 | 各向同性,精度有限 | 大面积刻蚀 | | 干法刻蚀 | 高精度,各向异性 | 成本高,设备复杂 | 高精度刻蚀 |
在上表中,我们对比了湿法和干法刻蚀的主要优缺点及其应用场景。这些信息有助于工程师在芯片制造过程中做出明智的技术选择。
代码块示例
# Python 代码示例:干法刻蚀模拟
def dry_etching(material, thickness, time):
# 刻蚀速率模型
etch_rate = {
'silicon': 1.0,
'oxide': 0.5,
'nitride': 0.8
}
# 检查材料是否在刻蚀速率字典中
if material not in etch_rate:
print("材料不在刻蚀速率字典中。")
return 0
# 计算刻蚀时间
depth = etch_rate[material] * time
return depth
# 使用示例
depth = dry_etching('silicon', 5, 10)
print(f"在硅材料上刻蚀了 {depth} 微米。")
在这个简单的 Python 代码示例中,我们模拟了干法刻蚀过程中材料的刻蚀深度。这有助于理解干法刻蚀的基本原理和参数控制。
通过本章节的介绍,我们了解了光刻与刻蚀技术的基本原理、工作流程以及优化挑战。湿法与干法刻蚀技术的比较与选择为芯片制造提供了灵活的技术路径。在接下来的章节中,我们将继续探讨芯片制造中的注入与金属化技术。
4. 芯片制造中的注入与金属化
在芯片制造中,注入和金属化是两个至关重要的步骤。注入过程负责将掺杂剂引入硅晶片中以改变其电学特性,而金属化则是形成芯片内部连接的关键工艺。本章节将深入探讨这两种技术,从原理到应用,再到最新进展,为读者提供全面的理解。
4.1 离子注入技术
4.1.1 离子注入的原理与过程
离子注入技术是一种利用高能离子轰击硅晶片表面,将掺杂元素引入硅晶体的制造工艺。与传统的扩散工艺相比,离子注入具有更高的掺杂精度和更深的渗透深度。其基本原理是通过电场加速掺杂元素的离子,使其以高速撞击硅片表面,从而取代硅晶格中的原子,实现掺杂的目的。
在本章节中,我们将详细介绍离子注入的物理过程,包括离子的加速、轰击、以及掺杂元素在硅晶格中的稳定机制。此外,我们还将探讨影响注入过程的关键参数,如离子能量、剂量、电流密度等,以及它们如何影响注入的深度和浓度分布。
4.1.2 离子注入的设备与参数控制
离子注入机是执行离子注入过程的关键设备。它主要包括离子源、加速器、质量分析器、扫描系统和真空系统等部分。离子源负责产生掺杂元素的离子,加速器则加速这些离子至预定的能量,质量分析器确保只有目标离子能通过,扫描系统使离子束均匀分布于硅片表面,而真空系统则提供必要的操作环境。
在本章节介绍中,我们将分析不同类型的离子注入机及其优缺点,并讨论如何精确控制注入参数以满足不同制造需求。例如,离子能量的控制决定了掺杂层的深度,而剂量的控制则影响掺杂浓度。
4.1.3 离子注入技术的最新进展
随着集成电路制程技术的不断进步,离子注入技术也在不断发展以满足更高精度和效率的需求。近年来,高能量离子注入、多重注入技术、以及低温离子注入等新方法和新技术被提出并应用于实际生产中。
在本章节中,我们将讨论这些新技术如何提高注入效率、减少晶体损伤、以及提升掺杂均匀性。此外,我们还将探讨离子注入技术在新材料和新结构中的应用,如FinFET和GAAFET等三维晶体管结构。
4.2 金属化(CVD与PVD)
4.2.1 化学气相沉积(CVD)的原理与应用
化学气相沉积(CVD)是一种利用气态前驱体在衬底表面发生化学反应,从而沉积出固体薄膜的工艺。在芯片制造中,CVD被广泛应用于绝缘层、导电层和阻挡层的形成。CVD过程通常在高温下进行,涉及复杂的化学反应和物质传输过程。
在本章节中,我们将深入探讨CVD的基本原理,包括化学反应的动力学、物质在气相和固相之间的传输机制,以及薄膜生长的微观机理。此外,我们还将分析不同类型CVD技术的特点,如低压CVD(LPCVD)、等离子体增强CVD(PECVD)等,以及它们在不同制程中的应用案例。
4.2.2 物理气相沉积(PVD)的原理与应用
物理气相沉积(PVD)是一种利用物理方法将材料从固态源转移到衬底表面的过程。与CVD不同,PVD不涉及化学反应,主要通过物理溅射或蒸发的方式实现材料的沉积。PVD技术包括蒸发镀膜、溅射镀膜等。
在本章节中,我们将讨论PVD的基本原理,包括蒸发和溅射的物理机制、以及薄膜生长的动力学过程。我们还将分析不同PVD技术的应用,如磁控溅射在金属化过程中的重要性,以及它们在芯片制造中的具体应用。
4.2.3 CVD与PVD技术的比较与协同
CVD和PVD各有优势和局限性,它们在芯片制造中的应用往往是互补的。CVD能够在较低的温度下实现均匀、连续的薄膜沉积,而PVD则更适合于高精度、高纯度的金属薄膜沉积。
在本章节中,我们将比较CVD和PVD在不同应用场合下的优缺点,并探讨如何结合这两种技术的优势以优化整体的金属化过程。此外,我们还将讨论在先进制程中,CVD和PVD技术如何协同工作,以及它们在新材料开发中的应用前景。
在本章节的介绍中,我们将通过具体的实例和数据分析,为读者提供对离子注入和金属化技术深入的理解。我们还将探讨这些技术在未来芯片制造中的发展趋势和挑战,以及如何通过技术创新来应对这些挑战。
5. 芯片后端工艺与验证
5.1 化学机械抛光(CMP)技术
5.1.1 CMP技术的基本原理
化学机械抛光(CMP)是一种用于平整半导体晶圆表面的技术,它结合了化学腐蚀和机械研磨两种作用。CMP的基本原理是在晶圆表面施加压力的同时,通过化学反应弱化晶圆表面的材料,然后通过磨粒的机械作用将材料去除。这种技术通常用于平坦化晶圆表面,以确保后续层的均匀性和高分辨率图案的复制。
CMP过程通常涉及以下关键步骤:
- 化学腐蚀 :使用含有磨粒的化学剂与晶圆表面的材料发生化学反应,生成一层易被机械去除的软质层。
- 机械研磨 :在施加压力的情况下,通过磨粒对表面的物理作用去除材料,达到平整化的目的。
- 抛光垫 :抛光垫在CMP过程中起到固定磨粒、均匀分配化学剂和提供机械研磨力的作用。
5.1.2 CMP的工艺流程与优化
CMP的工艺流程可以分为以下几个主要步骤:
- 预处理 :去除晶圆表面的微粒,减少CMP过程中的划痕。
- 上样 :将晶圆固定在CMP工具的载台上。
- 化学反应 :施加化学剂,开始化学腐蚀过程。
- 研磨与抛光 :施加压力,通过研磨盘和抛光垫的相对运动进行机械研磨。
- 清洗 :去除CMP过程中产生的残留物和化学剂。
- 干燥 :彻底干燥晶圆,为后续工艺做准备。
CMP的优化主要集中在提高均匀性、减少缺陷和提升生产效率。为此,CMP的工艺参数需要精心设计和控制,包括化学剂的浓度、磨粒的大小和类型、研磨盘的旋转速度和压力等。
5.1.3 CMP在先进制程中的应用挑战
随着半导体制程技术的进步,CMP技术面临着越来越多的挑战:
- 纳米级平整度要求 :随着特征尺寸的减小,CMP需要提供更高的表面平整度。
- 材料选择多样性 :新材料的引入,如低-k介电材料,对CMP化学品和磨粒提出了更高的选择性。
- 复杂性增加 :多层互连结构的复杂性增加了CMP工艺的难度。
- 成本控制 :CMP的成本控制成为晶圆厂关注的焦点,包括化学品的消耗和设备的维护成本。
5.2 封装测试与功能验证
5.2.1 封装技术的选择与发展趋势
封装技术是将芯片与外界接口连接起来的重要工艺,它不仅保护芯片免受物理和化学损害,还提供散热、电气连接等功能。随着芯片集成度的提高,封装技术也在不断发展:
- 引线键合 :传统的封装方式,通过金线或铝线将芯片焊点与封装引脚连接。
- 倒装芯片 :芯片面朝下与基板连接,减少封装尺寸并提高性能。
- 晶圆级封装 :在晶圆阶段完成封装,实现更高的集成度和更好的性能。
封装技术的发展趋势包括:
- 集成更多功能 :封装内集成无源元件,如电容、电阻等。
- 提高散热性能 :使用新材料和设计改善散热效率。
- 小尺寸化 :随着移动设备的需求,封装尺寸持续减小。
5.2.2 芯片测试的流程与方法
芯片测试是确保芯片性能和可靠性的重要步骤。测试流程通常包括:
- 晶圆测试 :在晶圆阶段进行初步测试,筛选出不良芯片。
- 封装后测试 :对封装完成的芯片进行全面测试,包括功能测试、参数测试等。
- 老化测试 :对芯片进行长时间工作,以评估其可靠性。
芯片测试的方法包括:
- 自动测试设备(ATE) :使用专门的测试设备对芯片进行电气测试。
- 边界扫描测试 :通过芯片内部的测试结构,检测芯片间连接的完整性。
- 功耗测试 :测量芯片在不同工作状态下的功耗。
5.2.3 功能验证的重要性与实施策略
功能验证是确保芯片设计正确性的关键步骤。在芯片设计阶段,功能验证的主要目的是通过模拟和仿真来检测设计中的错误。实施策略包括:
- 模块级验证 :对单个模块的功能进行验证。
- 子系统级验证 :验证多个模块协同工作的功能。
- 系统级验证 :在最终系统环境中进行验证。
功能验证的重要性在于:
- 减少成本 :通过早期发现问题,减少后续的修改成本。
- 提高质量 :确保产品在上市前满足所有功能要求。
- 缩短时间 :加速产品上市时间,提升市场竞争力。
为了进行有效的功能验证,通常需要使用专业的硬件仿真器和软件工具,如FPGA验证板和仿真软件。此外,通过建立完善的验证流程和策略,可以确保验证工作的系统性和全面性。
简介:本文详细介绍了电子行业中晶圆和芯片的生产工艺流程,是现代半导体器件制造的基础。从硅晶圆的生长到集成电路的封装测试,每一步都需精确控制以保证芯片性能和可靠性。工艺流程的不断优化,旨在提高芯片的集成度、速度和能效,满足市场日益增长的需求。
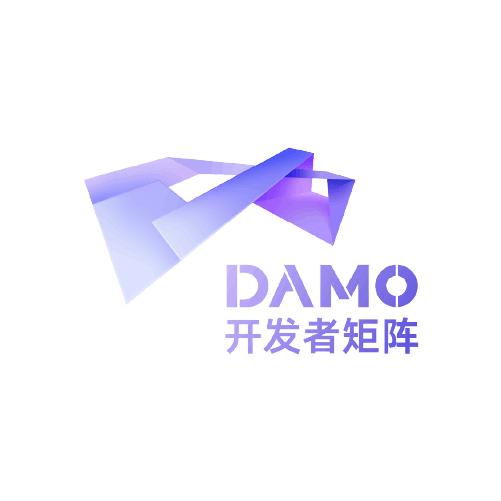
DAMO开发者矩阵,由阿里巴巴达摩院和中国互联网协会联合发起,致力于探讨最前沿的技术趋势与应用成果,搭建高质量的交流与分享平台,推动技术创新与产业应用链接,围绕“人工智能与新型计算”构建开放共享的开发者生态。
更多推荐
所有评论(0)